The Importance of Precision Molds in Modern Manufacturing
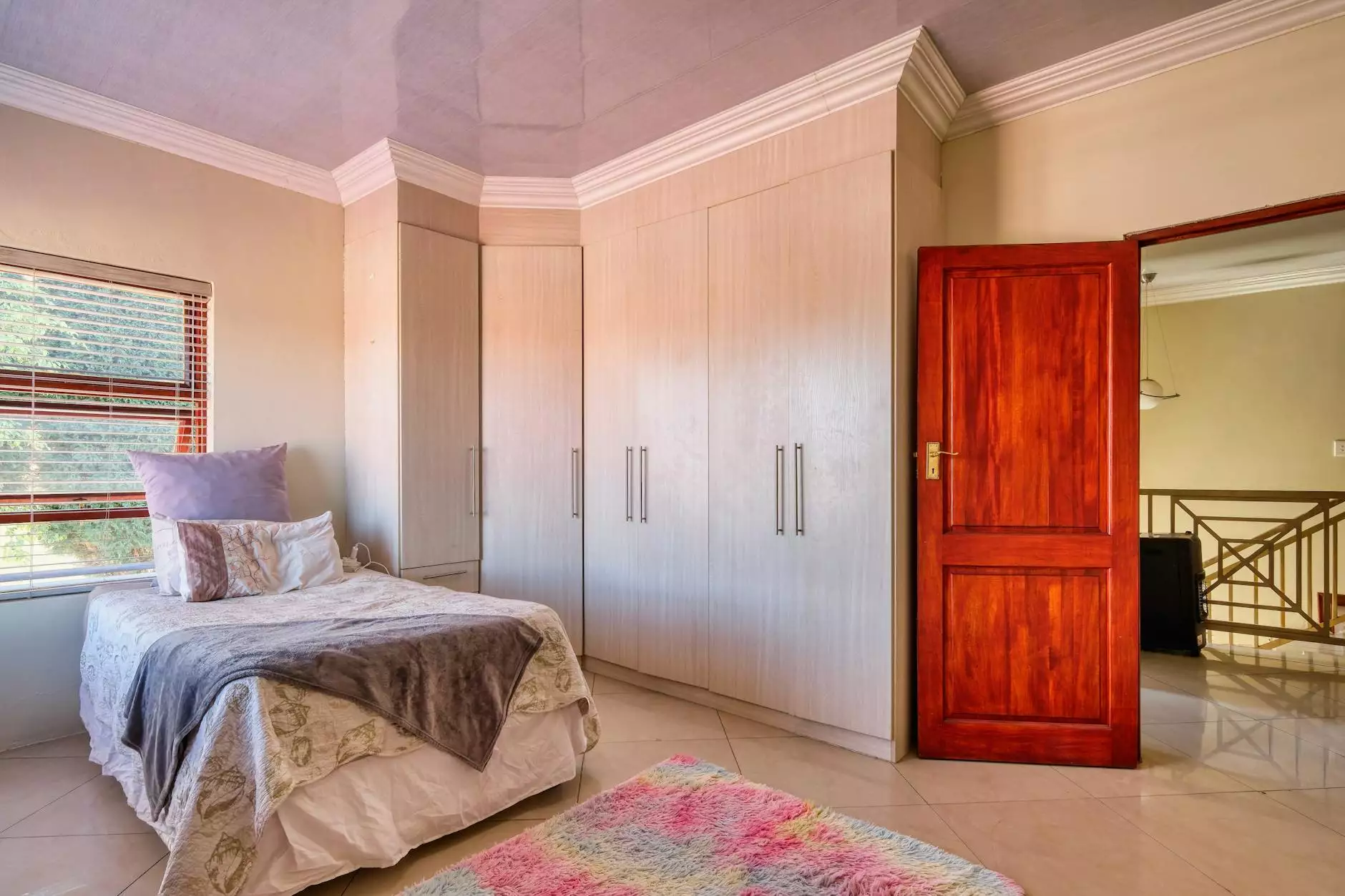
In today's fast-paced industrial landscape, the role of precision molds has never been more critical. These sophisticated tools are the backbone of manufacturing processes across various industries, including automotive, aerospace, consumer goods, and medical devices. As businesses strive for efficiency, scalability, and quality, understanding the nuances and applications of precision molds becomes essential.
What Are Precision Molds?
Precision molds are specially engineered components used in the manufacturing process to shape, form, and produce parts and products with high accuracy and repeatability. They are typically made from durable materials such as metals or high-quality plastics, designed to withstand the rigors of production while maintaining tight tolerances.
Types of Precision Molds
There are several types of precision molds, each serving specific purposes within the manufacturing domain. Here are some of the most common types:
- Injection molds: Used for injecting molten material into a mold to create parts, primarily in plastic manufacturing.
- Blow molds: Employed in the production of hollow plastic objects, such as bottles and containers.
- Compression molds: Suitable for forming thermosetting plastics and rubber by applying heat and pressure.
- Transfer molds: Allow for the heating and molding of plastic in a separate chamber before being transferred into the mold cavity.
- Die-casting molds: Used in metalworking to create parts with high precision from molten metal.
The Manufacturing Process of Precision Molds
Creating precision molds involves a series of meticulously planned steps. Here's an in-depth look at the process:
1. Design and Engineering
The first step in creating precision molds is the design phase, which involves using advanced software tools such as CAD (Computer-Aided Design) to create detailed blueprints. At this stage, engineers must consider the product specifications, material choices, and manufacturing methods to ensure optimal functionality and accuracy.
2. Material Selection
Choosing the right material for precision molds is crucial. Factors such as the intended use, production volume, and manufacturing conditions influence material selection. Common materials include:
- Steel: Durable and capable of enduring repeated cycles.
- Aluminum: Lighter and often used for prototypes or low-volume production.
- Bronze: Offers excellent wear resistance and is used in specific applications.
3. Machining
Once the design is finalized and materials selected, the machining process begins. This step involves various techniques such as milling, turning, and grinding to achieve the required dimensions and finishes. CNC (Computer Numerical Control) machines are commonly used for their precision and efficiency.
4. Assembly
The next stage is assembly, where different components of the mold are brought together. This requires precise alignment and fitting to ensure that the mold operates effectively during production.
5. Testing and Quality Control
Before full-scale production can commence, molds undergo rigorous testing. This includes running trial productions to observe the quality of the final products and identify any flaws. Quality control processes ensure they meet industry standards and specifications.
Benefits of Using Precision Molds
The adoption of precision molds in the manufacturing process comes with an array of benefits:
1. Consistent Quality
One of the most significant advantages of using precision molds is the ability to produce parts with consistent quality. The high accuracy achieved in manufacturing reduces defects and variations, leading to a reliable output.
2. Increased Efficiency
With precision molds, manufacturers can achieve faster production rates. The ability to produce multiple items in a single cycle, especially in injection molding, enhances productivity and meets market demands swiftly.
3. Cost-Effectiveness
While the initial investment in precision molds may be high, the long-term savings in material and labor costs are substantial. Enhanced durability reduces the frequency of mold replacement, thus lowering overall manufacturing costs.
4. Design Flexibility
Modern precision molds allow for intricate designs and complex geometries that would be impossible or cost-prohibitive to achieve with traditional methods. This flexibility opens up creative possibilities for product development.
Applications of Precision Molds Across Industries
The versatility of precision molds means they are utilized across a wide range of industries:
1. Automotive Industry
In the automotive sector, precision molds are critical for producing complex components such as dashboards, bumpers, and various engine parts. These molds ensure that every component meets strict safety and performance standards.
2. Aerospace Manufacturing
Aerospace components often require extreme precision due to the critical safety factors involved. Precision molds are utilized to manufacture parts like fuselage sections, wing structures, and interior components, ensuring they can withstand harsh conditions.
3. Medical Devices
In the medical field, the need for cleanliness and precision is paramount. Precision molds are used to produce items such as syringes, surgical instruments, and various disposable components, all of which require high levels of accuracy and reliability.
4. Consumer Goods
The consumer goods industry heavily relies on precision molds to produce everything from appliances to toys. The ability to deliver high-quality products in a cost-effective manner is essential in this highly competitive market.
Challenges in Precision Mold Manufacturing
Despite the myriad benefits, the manufacturing of precision molds is not without its challenges:
1. High Initial Costs
The upfront costs associated with designing and producing precision molds can be significant. Businesses need to balance initial expenditures with long-term benefits.
2. Expertise Required
Creating high-quality precision molds demands a skilled workforce and advanced technology. The need for expert machinists and engineers can limit production capabilities.
3. Maintenance and Repairs
Molds require regular maintenance to ensure optimal performance. Downtime due to repairs can affect production schedules, making it essential to plan for routine upkeep.
Future Trends in Precision Molds
The industry of precision molds is constantly evolving. Here are some future trends to watch:
1. Automation and Smart Manufacturing
As technology progresses, automation in mold making becomes more prevalent. Smart manufacturing processes and Industry 4.0 principles will enhance efficiency and reduce costs.
2. Advanced Materials
The development of new materials, including composites and advanced polymers, will expand the functionalities and applications of precision molds.
3. Sustainability
Manufacturers are increasingly focusing on sustainable practices, and the mold production industry is no exception. Innovations that reduce waste and energy consumption are expected to gain traction.
Conclusion
The importance of precision molds in modern manufacturing cannot be overstated. From enhancing product quality and production efficiency to reducing costs and fostering innovation, these tools play a vital role in a wide array of industries. As the market continues to evolve, staying informed about advancements in mold technology and practices will be crucial for manufacturers looking to maintain a competitive edge. Embracing the latest trends and investing in high-quality precision molds will not only improve operational performance but also contribute to long-term business success.
For more information on precision molds and how they can benefit your business, visit deepmould.net.