Unlocking the Potential of Injection Mold Plastics in Today’s Business Landscape
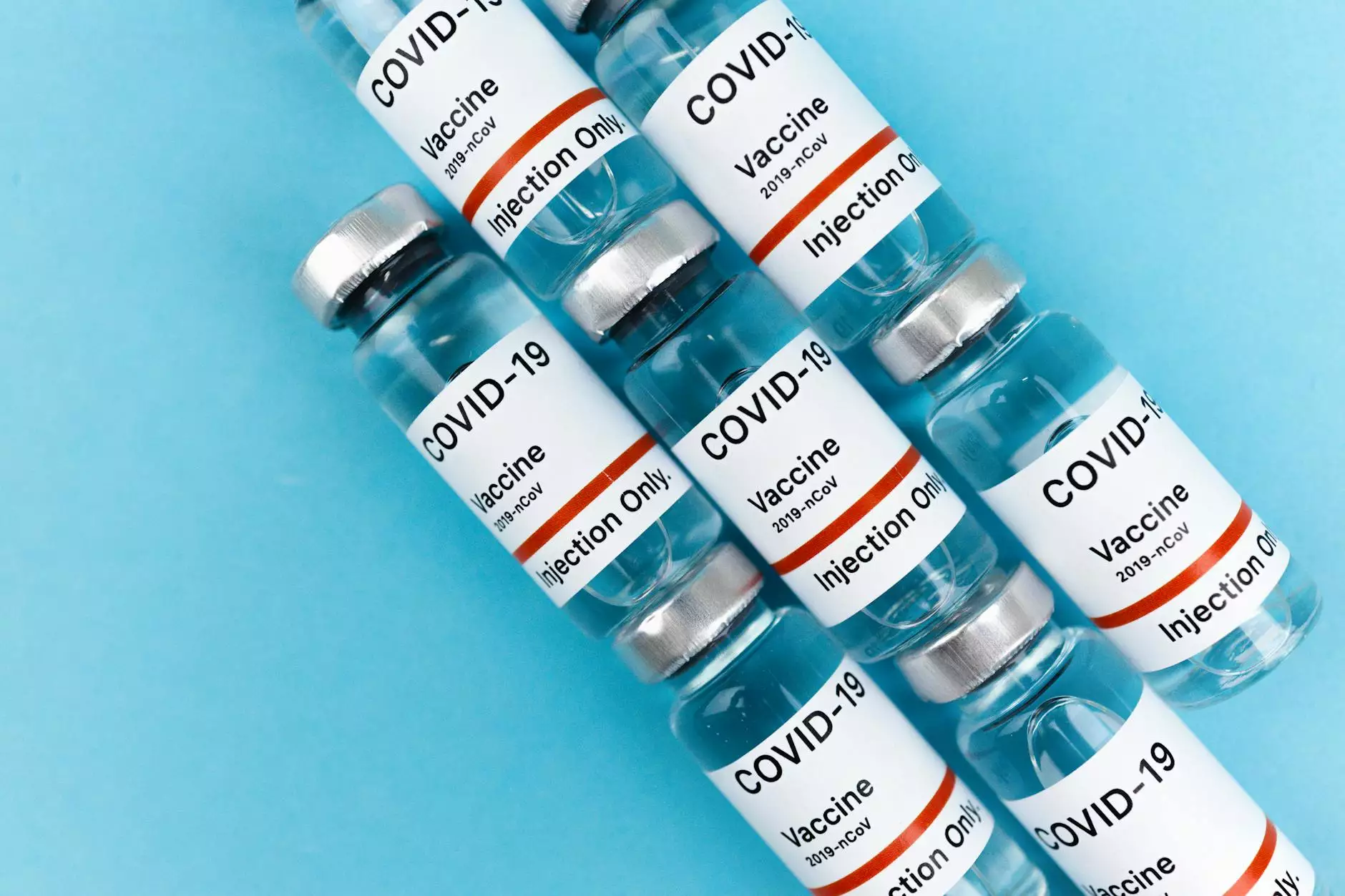
In the fast-paced world of manufacturing, the significance of injection mold plastics cannot be overstated. This technology has revolutionized the production process for countless industries, enabling businesses to deliver high-quality products while maximizing efficiency. In this comprehensive guide, we will explore the multifaceted applications of injection mold plastics, their benefits, and their impact on the landscape of metal fabrication and beyond.
What is Injection Molding?
Injection molding is a manufacturing process that involves the injection of molten material into a mold to create specific shapes and parts. This technique is particularly significant in the realm of plastics, where manufacturers can produce intricate designs with high precision. The process typically includes several stages:
- Material Selection: Choosing the right type of plastic is crucial for achieving the desired properties in the final product.
- Melting and Injection: The selected plastic is heated until it becomes molten and then injected into the mold at high pressure.
- Cooling: Once the material is in the mold, it is cooled to solidify and form the desired shape.
- Removal and Quality Control: The finished product is ejected from the mold, followed by rigorous quality checks to ensure it meets defined specifications.
Benefits of Using Injection Mold Plastics
Employing injection mold plastics in manufacturing comes with a host of advantages that can significantly enhance business operations:
- Cost-Efficiency: Injection molding is highly cost-effective for large production runs due to its speed and efficiency. Once the mold is created, producing additional units becomes increasingly economical.
- Precision and Accuracy: The molding process produces parts with tight tolerances and intricate designs that would be difficult to achieve with other manufacturing methods.
- Material Versatility: A wide range of plastics can be used in injection molding, including thermoplastics, thermosetting polymers, and elastomers, allowing for tailored properties to meet specific application needs.
- Reduced Waste: Unlike subtractive manufacturing methods, injection molding produces almost no waste, making it a more environmentally friendly option.
- Scalability: Businesses can easily scale production up or down based on market demand without expensive retooling.
Applications of Injection Mold Plastics in Various Industries
The versatility of injection mold plastics extends across numerous sectors. Here are some notable applications:
1. Automotive Industry
The automotive sector heavily relies on injection molded plastics for various components, ranging from interior parts like dashboards to exterior components such as bumpers. This reduces weight, enhances fuel efficiency, and allows for more complex designs.
2. Consumer Electronics
From mobile phone casings to intricate internal parts of devices, injection molding enables the production of lightweight and durable components that meet consumer demands for aesthetics and functionality.
3. Medical Devices
In the medical field, precision is critical. Injection molded plastics are commonly used in creating syringes, surgical instruments, and specialized devices where hygiene and performance are paramount.
4. Packaging Solutions
Injection molding allows for innovative packaging designs that are both efficient and sustainable. Companies are utilizing this technology to create custom packaging that enhances product protection and branding.
The Role of Metal Fabricators in Injection Molding
Metal fabricators are vital to the injection molding process, primarily through the production of molds. High-quality molds are essential for ensuring that the final products meet rigorous quality standards. The relationship between metal fabrication and injection molding is integral to the success of various manufacturing businesses.
Collaboration for Custom Solutions
Metal fabricators often collaborate with plastic manufacturers to create custom molds tailored to specific product requirements. This partnership drives innovation and allows for the rapid development of new products. The intricate designs achievable through precision metalwork help businesses stand out in a competitive market.
Innovations in Injection Mold Plastics
As technology advances, the field of injection mold plastics continues to evolve. Some of the key innovations include:
- 3D Printing for Prototyping: Rapid prototyping using 3D printing technologies allows manufacturers to quickly test designs before committing to full-scale mold production.
- Advanced Composite Materials: The introduction of composite materials in injection molding can lead to stronger, lighter products that enhance overall performance.
- Smart Manufacturing: The integration of IoT and AI in the production process allows for real-time monitoring and optimization, improving efficiency and reducing downtime.
- Sustainable Practices: As sustainability becomes increasingly important, many manufacturers are exploring biodegradable plastics and recycling opportunities to minimize their environmental footprint.
Challenges in Injection Molding
Despite its many advantages, injection molding also comes with challenges that businesses must navigate:
- High Initial Costs: The upfront costs for designing and producing molds can be substantial, making it a less attractive option for small production runs.
- Complex Design Constraints: While injection molding allows for intricate designs, very complex structures can be difficult to produce consistently and may require skilled professionals.
- Material Limitations: Not all materials are suitable for injection molding, limiting options for specific manufacturing needs.
Best Practices for Effective Injection Molding
To maximize the benefits of injection mold plastics, businesses should adhere to best practices:
- Thorough Planning: Detailed planning of production processes, from mold design to material selection, can streamline operations and reduce costs.
- Continuous Testing and Quality Control: Implementing rigorous testing protocols ensures that all products meet necessary standards and specifications.
- Investing in Technology: Upgrading to the latest technology in molding machines and processes can enhance efficiency and quality.
- Collaboration with Experts: Partnering with experienced metal fabricators and mold designers can lead to innovative solutions and improved product designs.
Conclusion: The Future of Injection Mold Plastics in Business
In conclusion, injection mold plastics serve as a cornerstone of modern manufacturing, offering unparalleled advantages in efficiency, precision, and versatility. As industries continue to evolve, embracing innovative practices and technologies will be essential for businesses that wish to thrive in a competitive landscape. By leveraging the capabilities of injection mold plastics and collaborating effectively with metal fabricators, businesses can unlock new opportunities and drive significant growth. The future is bright for those who harness the potential of this transformative manufacturing method.
Contact Us
If you are interested in leveraging injection mold plastics for your business, or if you seek high-quality metal fabrication services, reach out to us at deepmould.net. Our team of experts is ready to assist you in bringing your ideas to life with precision and efficiency.